By Dr. Felix Ramshaw, Ph.D. (Post-Human Yield Management & Digital Agronomy)
Department of Algorithmic Crop Sciences and Mechanical Livestock Affairs, Baitman’s Institute
Published in the Journal of Autonomous Farming Systems and Embedded Soilware, May 2025
Abstract
A controlled, multi-phase study conducted on the historic Wormsworth Estate Experimental Fields—a once-aristocratic parcel of land donated to the Institute by descendants of the Wormsworth family in lieu of taxes—has revealed promising results in the race to automate agricultural labor. The site, which now serves as both an educational facility for Baitman’s agriculture students and a flight testing range for the Institute’s drone trades program, offers unique logistical challenges. These include altitude-tier scheduling, air-to-ground conflict mitigation, and enforced “drone corridors” to avoid repeated entanglements with experimental autonomous harvest vehicles.
Prior efforts in automated farming at the Wormsworth campus zone include notable failures such as the SapienScythe, a machete-wielding biped robot decommissioned after a corn maze incident, and the AutoMoo-2, a cow-milking unit that achieved a 4% success rate and one student lawsuit. Yet progress marches on.
In this latest trial, five prototype agri-robots sourced from international vendors were subjected to comparative performance testing in live crop environments. Originally conceived as a data-driven robotics trial, the event gradually took on a more ceremonial tone as spectators arrived—lawn chairs in hand—for what ultimately became known as the Autonomous Agricultural Field Olympics.
Introduction
As global labor markets contract and rural workforces dwindle, the promise of artificially intelligent farming systems has generated intense interest. In particular, the prospect of replacing low-wage immigrant labor with complex machines built out of lithium, sensors, and plastic sourced from deeply unregulated e-commerce platforms has ignited both policy excitement and institutional grant activity.
Recognizing the geopolitical and technological stakes, the Baitman’s Institute launched a comprehensive field evaluation of available AI-powered farm worker units. These units, acquired via subsidized bulk orders from various international distributors, represent the cutting edge of what countries not bound by robust safety standards are currently able to produce.
To maintain scientific objectivity, all units were subjected to identical environmental conditions, crop loads, and observer proximity. Timmy (age 12¼)—the only local resident with a functioning drone, after a 2023 incident involving a crop duster and the entire school’s DJI fleet—was contracted as the aerial documentarian for the study. Judging was performed by an impartial panel consisting of Becky (HR), Carl (Campus Security), and Otis (Janitor), each selected for their unique approach to fairness, skepticism, and silence.
Robot Descriptions & Technical Specifications
Model Name | Country of Origin | Manufacturer / Platform | Core Features | Known Issues |
---|---|---|---|---|
AgroFriend Z9 | China | TEMU-Agritech™ | Suction-based berry retrieval, Lidar arms | Swings at birds if battery low |
Shigoto-X900 | Japan | ZenHarvest Robotics | AI pick-recognition, haiku interface | Soft resets every 88 minutes |
Gruboslav-7 | Serbia | TeknoPolje Systems | Two-stroke motor, steel claws | Picks soil with equal enthusiasm |
Swilitech Nomad | Swililand | Swilitech Labs | Solar backpack, Bluetooth antenna tail | Believes all crops are state-owned |
Lettucer™ R2 | South Korea | eSalad.me Industries | Dual-arm leafy crop sorter | Loudly announces “LETTUCE LOCATED” |
Each unit was programmed with basic agricultural task parameters using a universal translational interface designed by Intern Daniel, who claims to have “mostly figured out C++” over spring break. Units were assigned randomized tasks within identical crop sectors: strawberry beds, lettuce rows, and an old irrigation field overtaken by rogue arugula.
Methodology
The robots were evaluated across three primary functional areas:
Harvest Precision
Measured by number of viable crops collected per minute
Non-viable harvests (dirt, rocks, hats, Carl’s lunch) were deducted
Mobility / Pathing
Efficiency in row navigation, obstacle detection, and panic response
Carl stood in the field randomly to “simulate rogue conditions”
Packaging & Output Readiness
Robots were expected to place harvested crops in provided bins
Points deducted for attempts to “eat,” destroy, or replant produce
All tests were monitored live from the Otis Observation Hill, an elevated berm formed from leftover gravel and compost, with visibility of all robot lanes and adjacent spectator zones.
Development into Spectator Event
As testing entered its second hour, word spread across campus. The Spirit Club arrived with a folding table and kazoos. Students and unaffiliated townies followed, bringing coolers, binoculars, and in one case, a BBQ smoker.
By mid-afternoon, the Institute had de facto launched the Autonomous Agricultural Field Olympics™—an informal but highly energetic contest of robotic labor prowess. Otis quietly chalked lanes into the grass. Carl erected caution tape “just to be safe.”
Official Events & Performance Table
Event Name | Winner | Spectator Notes |
---|---|---|
Strawberry Running | AgroFriend Z9 | Fastest, but damaged 48% of strawberries |
Lettuce Harvesting | Lettucer™ R2 | Efficient, though extremely loud |
Packaging & Bin Toss | Shigoto-X900 | Graceful, presented one head of lettuce with a bow |
Row Navigation Sprint | Gruboslav-7 | Bulldozed through two fences, no hesitation |
Freestyle Arugula Pull | Swilitech Nomad | Refused to stop. Declared field “liberated” |
Scoring remained controversial. Becky used a laminated rubric. Carl refused to acknowledge AgroFriend’s “repeated berry assault incidents.” Otis submitted no notes, but repositioned his chair closer to the Swilitech unit and stayed there until sunset.
Outside Considerations
While the performance of autonomous farming units was mixed, it’s important to contextualize the results with existing data. Multiple agricultural policy studies (e.g., USDA labor reports, UC Davis migration research) confirm that immigrant field workers remain among the most efficient and cost-effective labor forces in modern agriculture. With average harvest speeds exceeding mechanical alternatives in diverse crop types, many analysts argue that streamlining the U.S. immigration and seasonal work visa process could resolve the labor crisis far more easily than constructing multilingual lettuce bots.
However, as Dr. Ramshaw noted during post-trial interviews, “policy reform is a slow-moving plow. But lithium? That’s fast and ready to ship.”
Conclusion
The Wormsworth Trials mark a critical inflection point in agricultural engineering. While none of the participating robots could entirely replace a skilled human worker, each demonstrated intermittent competence, occasionally doing the right thing for nearly a full minute at a time.
Therefore, this study concludes that—given enough silicone, sensors, batteries, and aggressive international ordering—the agricultural labor crisis can be mitigated by machines. At least partially. Perhaps tomorrow. Or the next day. Depending on shipping.
Sources
“Robots in Agriculture: Adoption and Limitations” – AgriTech Futures, 2024
Interviews with undocumented workers in California’s Central Valley (summarized in Labor Without Borders, UC Davis)
The user manual for the Gruboslav-7, translated from Serbian with Google Lens
Spirit Club Facebook Live recording, comment section
Otis (no direct quote; stood meaningfully near lettuce bin)
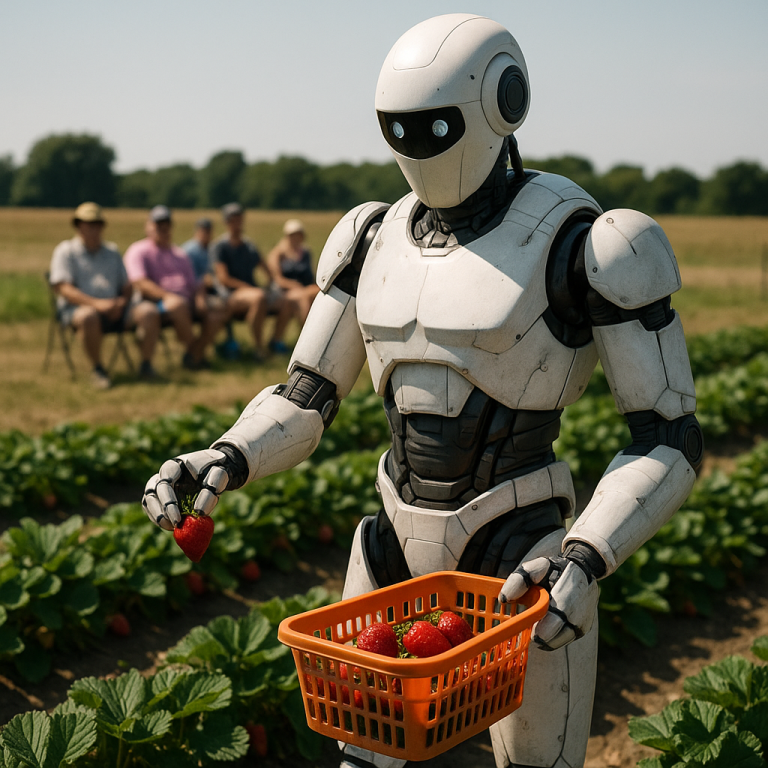